Shattered Dreams
When it was “Finally” launched in 2012 (already 5 yrs. behind original schedule) everyone thought that it would change the way the world flew and allow airlines to save a lot of money transporting people and goods across the planet on the Dreamliner 787 series, which were touted to be 20% more fuel efficient and with higher carrying capacity. The launch was so amazing that it was actually launched by none other than the US president (Obama) himself.
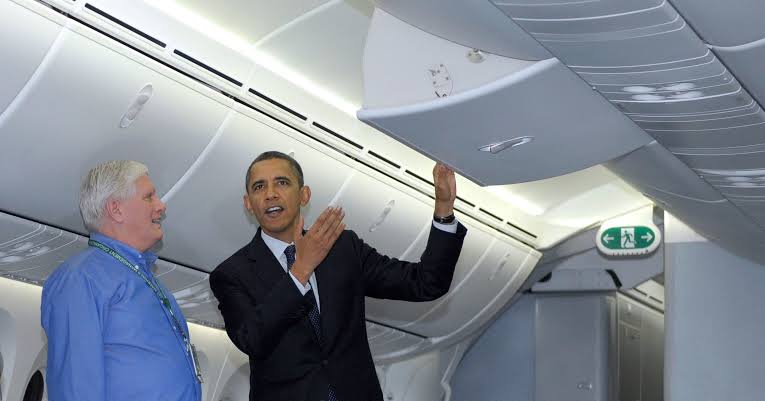
However in 2013 the entire fleet of Dreamliners 787 were grounded due to horrendous and surmounting problems and issues. Issues that had origins during the Project Management and issues that were part of operations, both cast a shadow so huge that the Dreamliners became a Nightmare for all airlines that had bought them.
Fortunately, after a lot of rework, at a cost that almost made the company Boeing bankrupt, the 787 are back in the skies, covering some of the longest routes but a lot fewer in Numbers than originally estimated and now it would never ever reach those numbers. Though Dreamliners continue to fly now, they have, forever been associated with “Failed Project” and an “Unsafe Aircraft”. An association that still persists in 2019.
PM-Pulse brings you the inside story of the Project Management goof-ups done during the development.
Two of the most successful aircrafts of Boeing viz., 747 series and the 767 series were getting old and expensive to maintain for both, client airlines as well as Boeing. Airbus was already rushing forward to fill that gap by promoting their Airbus A380 and a lot of airlines were showing serious interests. Boeing decided to create a drastically different aircraft that would be simply more fuel efficient to the extent of 20%. This meant that the aircraft industry would line up to them as this aircraft could save them a lot of money while carrying same amount of load and for longer durations. And yes, airlines did line up in huge numbers, well at-least till 2013.
Period 1992 – 2000 : What lead to the idea of Dreamliner 787.
Between early to mid 1990s Boeing realized that despite the amazing success of their aircraft 777, it was the Airbus that was making the profits. Boeing was struggling with maintenance issue associated with an aging aircrafts line linked to the agitated airlines that were getting increasingly frustrated with Boeing aircrafts.
Boeing decided to “Win back” the market by producing “Faster aircrafts” that would use the same amount of fuel while carrying the same amount of load as their fleet of 767s. Boeing spent a fortune in producing a concept of “Sonic Cruiser” which would be 15% faster than any commercial aircraft. This sounded great and many airlines showed interest.
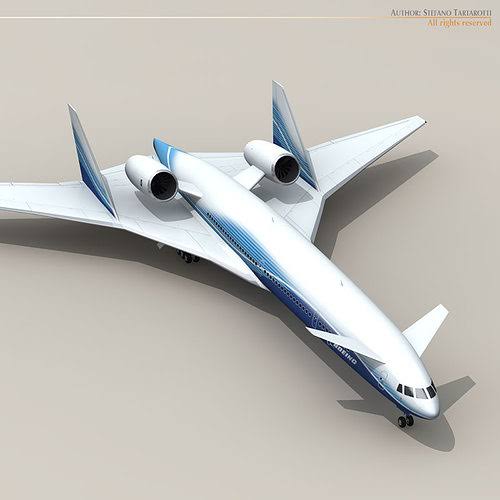
However by mid 2000 and early 2001 it was clear that more airlines were interested in “Fuel efficiency” rather than “Speed”. This change in perspective almost completely nullified all the development cost undertaken during the last decade which had resulted in a working concept which the market did not need anymore.
From the ashes of this debacle, rose the concept of the “Carrier 7E7” which was later renamed as “Dreamliner 787”.
Project Initiation:
With severe management changes in Boeing’s Board of Directors and with the acquisition of McDonell Douglas (essentially a fighter aircraft development organization) a lot of new ideas and concepts entered the Boeing organization.
Boeing finally decided, in mid 2003, to start the development work on the “Dreamliner 787” project. The Sponsor Directors made a few clear mandate which can be listed as under: -
-
Aircraft to provide better climate control and higher in-flight humidity along with comfort to the passengers than any other aircraft.
-
Make the aircraft so light (and yet durable) that it consumes 20% less fuel than any other aircraft.
-
Make the aircraft designed to travel ultra-long distances thus allowing a dynamic change of roles and configurations for the aircraft by the airlines.
-
Make the aircraft so configurable to a variety of seating plans that the airlines could change them faster than any other aircraft in the world.
-
Reduce the cost of development of this new aircraft by getting the vendors of parts to bear some of the development costs, which in turn were to be offset by getting continued manufacturing orders during operations. The target was arbitrarily caped at 40% of the development cost spent on 777 (which happened 13 yrs prior to the project initiation date).
All this would ensure that the “Dreamliner” becomes the largest selling aircraft on the planet. The kind of response that Boeing received from Airlines, gave all indicators supporting this target.
Project Planning
One of the most amazing part of the project planning was that there were no clear Program Directors appointed. The senior directors from McDonell Douglas were given the charge and they directly started working with engineering heads of various functions.
The planning was done with almost total focus on the concept of “Planning for Outsourced and collaborative Development” rather than “project planning”. This means that the entire project was divided into parts and further into components which would be outsourced to different vendors, who would spend their own money to “Develop” these components and then at an appointed time, all the components would be put together to assemble a “Revolutionary Aircraft” that would be better than any aircraft in the world in it’s category. This meant that the development of components by the vendors would be in parallel with the “Concept and design development” by the Boeing R&D team.
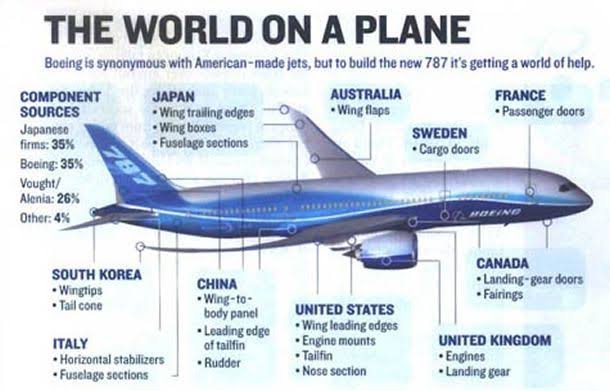
This method, being common method of developing military aircrafts in McDonell Douglas, the directors were bullish on implementing the same style of development in the Dreamliner Project of Boeing.
Design Concept work started and soon all the necessary vendors were identified and selected. They were selected based on their R&D capabilities and how much of their own money they were ready to invest in the development of components irrespective of how far and geographically distant they were.
One of the crucial management decisions taken was that no vendor or Boeing officer would physically travel to any of the vendor locations and vice versa. Instead they would use the best of “Virtual Team Collaboration” tools that existed in the market and thus save handsomely on the project development overheads.
Soon the creativity and technical brilliance of the Boeing R&D and some of the leading Vendors started to show results. Some of the most amazing ones were:
-
Constructing the entire body of the aircraft as a “seamless tube” (very much like the toothpaste tube) made of composite material (instead of aluminium) thus making the aircraft lighter and yet durable.
-
By replacing aluminium sheets with composite material, the cabin could maintain better pressurization and higher humidity that would provide better comfort to human body even during longer haul flights. (Something not possible with Aluminium sheets).
-
Using a high powered “Lithium-ion” battery for all inflight instrumentation, climate control and aircraft controls, instead of using power from engines, thus making the aircraft even further fuel efficient. (The first aircraft to have this rather risky feature)
-
Lighter seating material and electronics that would provide unparalleled flight comfort and in-flight entertainment options to the passengers.
-
Working with vendors from different countries thus making those countries more open to buying Boeing Aircrafts, e.g., getting the Lithium-ion” batteries and Wing assembly from Japan ensured a pre-order of 50 787’s by ANA of Japan.
-
Development budget USD 6 Billion.
July 8, 2007 – first 787 unveiled at Boeing’s Everett assembly factory, with 677 orders already received. Initial plan is for aircraft to enter commercial service in May 2008.
The work started with a lot of gung-ho and good cheer. Little did anyone in Boeing know that all of that would change in just 2 to 3 yrs.
Project Execution and Control (Project Implementation):
The design problems and the misunderstanding of scope of work for each vendors, started from the word go. Vendors were enthusiastically doing a lot of R&D at first but soon Boeing realized that several vendors were involved in “R&D of similar components” for the overlapping portions that were not clarified by the Boeing. Boeing shut down some of the development work as redundant, which resulted in loss to the vendors due to wasted effort that they have no hope of ever recovering. Some of the vendors, like Alenia, the subcontracting organization building the tail section reported a total loss of Euro 70Million by 2013.
The original idea was that even the sub-assemblies of the parts made by vendors, would be done at the vendor site, allowing the assembly plant at Washington to reduce the assembly time from 3 months to (theoretically) 3 days. This never ever happened.
The confusions kept mounting and deliveries of parts kept getting delayed. The Assembly workers and engineers at Washington were one of the most harassed team who had to end up finishing the unfinished work of the vendors to make the components fit together. Several components, though perfect in dimensions, were incompatible to fitting due to different standards of final fitting dimensions and processes. This meant that the assembly team had to undertake a lot of “Work-arounds” to somehow get the components fitted. Something that turned out to be the reason for Dreamliner undoing much later in the lifecycle.
The project status meetings, which were mostly virtual, ended up being a finger pointing contest and full of acidic acrimony. People were fired on the spot and several engineers, both from Boeing side and Vendor side resigned during such “Slig Fest” contests in the name of “Status Meetings”.
The first 10 assembled units were grossly overweight. Boeing tried to sell them but the airlines kept deferring their purchases to later more lighter units. These first 10 units resulted into a total loss for Boeing.
Their first flight, which was to take place in May 2007 which kept on getting delayed a quarter at a time to finally take place in December 2009. Several airlines had, by then started closing down their orders or reducing the number of units ordered.
Serious project issues were encountered the moment the first flight was conducted, like Inability to handle bad weather, problems with passenger window stability during high altitude flight, and serious issues with the horizontal stabilizers. This resulted in serious changes and upgrades to all the units produced and massive change request to the rest of the units under development.
The second test flight resulted into an in-cabin fire due to several faulty and untested wiring assemblies. This resulted into yet again a heavy change request for the entire fleet of “under-development” units and assembly units. This put tremendous pressure on the timelines and the budget. Some of the vendors decided to leave the program due to unsustainable losses with no hope of recovering the same in future. This resulted in more pressure due to selection of a new vendor and the troublesome technology transfer.
All this while, the management at Boeing was very acidic to any inputs from the engineering staff. When one of the senior most quality technicians voiced concerns over the electrical wire assemblies and battery volatility, he was simply asked to sign the “Tested Ok” form so that the Aviation regulation body (FAA) could approve the same, and later fired that engineer.
During the 2008 -2009 downturn, Boeing cancelled most of the worker bonus, but during bailout by the government, paid the directors massive incentives, without any of the bailout reaching the workers. This resulted in a massive paralysing strike of work at Boeing assembly plant.
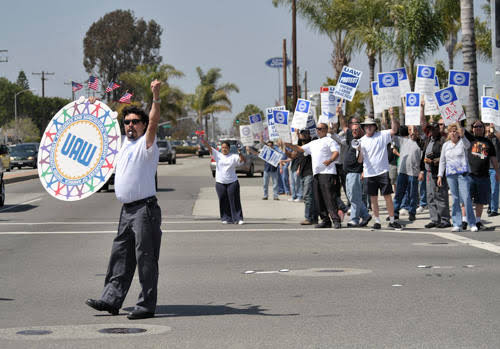
The specifications to the Revolutionary engines changed so many times that the final engine from Rolls Royce had to be repaired several times for the very first batch of 5 aircrafts that ANA had already bought and commissioned. This fact leaked out and more airlines cancelled their orders.
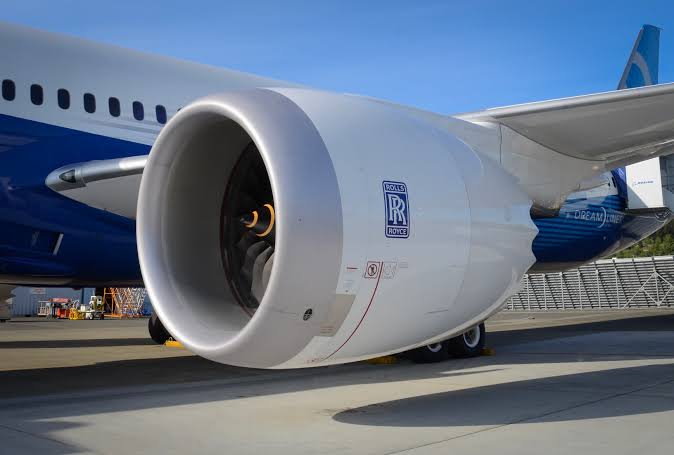
Almost every possible issues one can think of, from cockpit window popping open, to hairline cracks on the fuselage, from plumbing blockages in washrooms to fires in electrical fittings, from fuel leakages to fire in a parked and empty aircraft at hanger.
When such issues were being reported by clients and media, instead of accepting the issues and vowing to resolve them, Boeing resorted to denying them, avoiding them and even disbelieving them. This made everyone even more suspicious of Boeings intent and adherence to quality processes.
Finally to top it all, one of the ANA 787 aircrafts had a battery burnup while in flight leading to an emergency landing. This lead to aviation regulators to ground the entire fleet of 787’s as well as halting the development and assembly of 787s under construction till the matter was resolved.
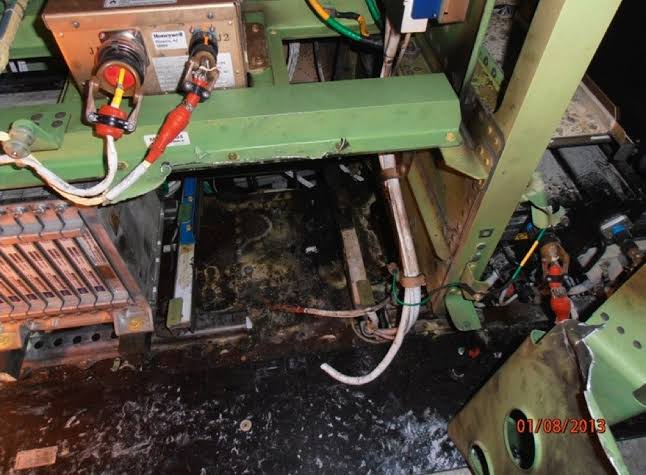
During this time, one of the investigative journalists, used a hidden camera to interview and record the emotions and words of the engineers working at the Boeing’s Washington assembly plant. The crux of that report was that none of the Boeing engineers and senior management ever flew in a 787 due to the fact that they themselves felt that it was a seriously dangerous aircraft owing to the liberties they were made to take with quality, safety and structural soundness in the hurry to release the aircrafts into the market.
The news coverage of all these disastrous issues caught the eye of the Aviation authorities who appointed a “Regulator” to ensure that Boeing fixed all these problems. This regulator was the same person who had signed the approval of allowing an aircraft to have a Lithium-ion battery (something no allowed ever on aircrafts) and he “seemingly” spent 123 days going through each and every aspect of the 787 and then signed it back as “Approved”. What later happened is that the same Regulator resigned from Aviation authority (FAA) and started working for Boeing as a VP and lobbied with FAA to allow “Delegation” of “Regulations” to Boeing.
Now, seemingly, most of the problems of 787 have been addressed by Boeing they are back in the skies but are definitely not selling anymore. There are no more development and no more construction of these aircrafts.
Final cost of development of 787 Dreamliner was pegged at USD 44 billion. Boeing continues to loose over USD170 Million for each aircraft sold and as of today out of the total order of 1,455 some 906 were actually delivered and out of those about 100 or so are not used by the airlines and several hundred of those in active service face serious maintenance issues which an impoverished Boeing finds harder and harder to fix.
At the time of writing this blog (November 2019) while Boeing struggles to maintain its organization after the Boeing MAX debacle along with Dreamliner 787 debacle, there are fresh allegations on Boeing about bribe, cutting corners in safety measures as well as obtaining FAA approvals using dubious methods. All these allegations are being made by workers and engineers of Boeing assembly plat.
Two more serious cases of Engine Trouble have been reported by Singapore Airlines and Jetstar. Singapore has grounded 2 787 Dreamliners. This has started another round of investigations for Boeing because these issues were “Supposed” to have been solved by Boeing and duly approved by FAA.
This saga of “Shattered Dreams” goes on. Hopefully no further disaster happen again or no further life are lost.
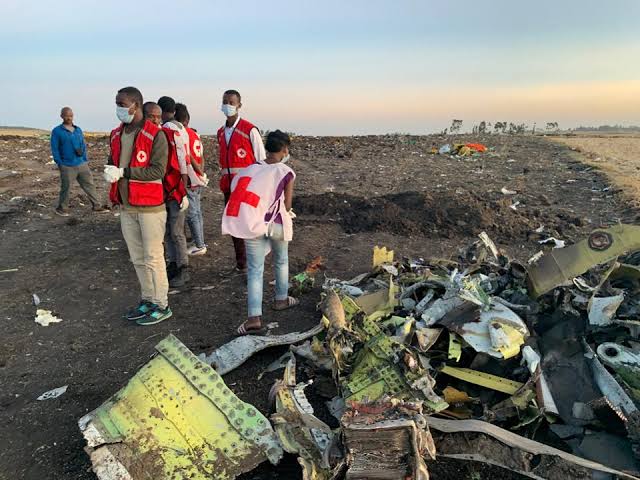
Lessons to be learned: -
-
A good idea is not always a workable idea, The idea needs to be developed with due process and after taking inputs from all participants.
-
Business case is needed but technical feasibility is also just as important.
-
No matter how much of experience you have in the past, there is no substitute for serious and practical Risk Management
-
Just articulating lofty targets is not the same as planning.
-
Firefighting may look glamorous but eventually ends up ruining the project
-
Lessons learned is a continuous process and project team must ensure that mistakes are never repeated during the project and these lessons must also become part of the handover to operations.
-
Management needs to develop team and not to bark down at them when they need management’s guidance the most.
-
Just because an idea works under different condition, different market place and different stakeholders it does not necessarily mean that it could be applied “as-is” to a different set of conditions.
-
Outsourcing should not be done at the design stage.
-
Outsourcing should be done with proper scoping and clarity of roles and responsibilities.
-
For projects that are connected to safety and security, schedule and budget must never be given more priority over scope of work.
-
Never discount the feedback coming in from the project team as they are closest to the real work.
-
Just investing in fancy tools for Virtual Teams does not necessarily produce a great productive virtual team. Managers have to work towards building a team.
-
Workarounds and quick fixes tend to be more expensive for the organizations and projects in the long run.
-
An hour of planning saves 100 hrs of execution.
-
No matter how big or famous you are, you cannot rely on just your organizational name to sail through the project deployment.