As I conduct trainings and consulting sessions across various geographies on the subject of project management I do see a recurring pattern of confusion about certain terms connected to Quality, namely, Precision, Accuracy and Excellence. Sometimes people try to include these terms in the very definition of Quality itself thus resulting into professional tragedy at various levels.
Though these terms are connected to the overall concept of Quality, they are never ever used in defining the term quality (unless you are using Wikipedia to understand the term Quality). Using Wikipedia to understand management terms is a colossal tragedy in itself.
Let me first clarify exactly what these terms mean and then I will go on to explain their practical relevance using real world examples to ensure that you not only understand this term well but also be able to use them in real world and become practically more effective.
Let us look at the term Precision, first. The closest other term that could be used in explaining Precision is “Consistency”. The official definition of Precision is “Lack of variance in measurements” or “Lack of degree of variances in two or more occurrences of an event”. While you may still find this definition unclear, one thing to notice here is the presence of terms like “consistency” and “lack of variance” and the absence of words like “exact” and “accurate” from the definition.
I was in National Cadets Core (NCC) where we had three levels of qualifications viz., 1, 2 and 3. During the levels 2 and 3 we were given a lot of practice for shooting guns (some of them rather antiquated ‘”Short Magazine Lee Enfield” bolt action gun) on to a paper target placed at varying distances. One of the biggest challenges with these rifles were that they had a very “Dodgy” (well if the gun was from England, its appropriate that I use an English slang for “Unreliable”) sight system. The sight system tended to go off alignment by just a fraction of mm but this resulted into a sizeable difference when we looked at bullet holes on the paper target. Hence our commander always gave us 10 to 15 bullets (always a multiple of 5 and to be shot in groups of 5 shots for each target) and asked us to get our shots as close to each other as possible, irrespective of where they hit on the target. He actually dissuaded us from trying to hit the bull’s eye. I was one of the cadets who shot very consistently and always qualified. Once he saw that my shooting was grouping very well he would say, “Cadet, that is some precise shooting, keep it up” and give me my next challenge. He would keep a record of all the cadets who shot close-groups and then always asked where we were “Aiming at” on the target. Having had that information he would go to work on the target with callipers and rulers to see the distance from where I was aiming and where the bullets hit and would adjust the sights with an oversized key shaped “Screwdriver” and then he would ask us to “Aim for the Bulls-eye”. We realized that in most cases we could get all our 5 shots into the bull’s eye. Some guns needed one more round of adjustment before it could get to shoot straight. He made our small group of shooters shoot from every single gun so that by the time we were through, all the guns were “Zeroed” or “Sighted In” (meaning it would shoot exactly where it was aimed at).
What needs to be seen here is that in the real world “Precision” is more important than accuracy. This is not only true for rifle shooting but in just about everything in the world including project management quality processes.
Let us say you are producing 1 million soaps a day. You have implemented processes that should give you less number of rejections post-production. Let us say that the “Process Benchmark” is an accuracy level of 80%. Which means not more than 20% of the total produce would be rejected at retail. However when you did a detailed analysis of the “Rejections in the previous month” you realized that you are consistently getting rejections at 50%. This is a terrible loss and obviously something is seriously wrong with your “Quality” processes. Now let us take the example of another organization which is making soaps and is your arc-rival in the local market. They produce around 800,000 bars of soap each day and your market research shows that they sometimes have just 1% rejections and sometimes 10% rejections and at times 45% rejections. The question here is whose “Quality Process” is superior, your or your rivals.
This tends to be a tough question and most of us will suggest that “obviously” it is the process of your rival that is superior. Not True. Wrong. It’s your process that is far more superior to your rivals. The thing is that your process has consistency, even if it’s consistently going wrong. Your rivals’ processes is rather unpredictable and inconsistent and seems to be accurate by chance and not by choice. There is no doubt that you will do a “Cause and Effects Analysis” of your process or even initiate a six sigma improvement project for your process. It would be easier to find the cause of a process that is consistently going wrong and once corrected it tends to go consistently right. Consistency is the key here. If any analysis was done for the rival’s processes, there would be no way to find out what is wrong with its process as it is inconsistent and unpredictable. A process which is consistently wrong can be corrected but a process that is accurate by chance can never be corrected or improved and would have to be replaced.
I guess you might be having an “Aha” moment now.
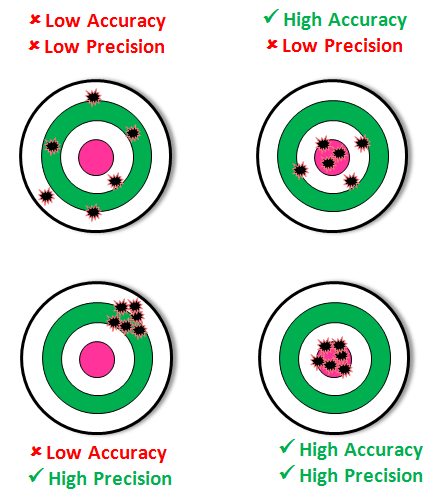
“A consistently wrong process is much more mature than a process that is accurate by chance.” ©PM-Pulse 2017 Authored by Maneesh Vijaya, PMP.
Consistency always comes before accuracy. Accuracy is a by-product of consistency.
Unfortunately, in the real world, managers and executive end up appreciating processes which are Accurate by chance without even investigating the consistency trend. In most organizations, if a project finishes close to the target it would be made into a template for all other projects following the processes in that project, blindly. Guess what the results are. And when the projects do not give the expected results the management starts blaming the “Ownership” of personnel or the “Culture” of the organization. No analysis is done about the consistency of processes or project practices. The basic misalignment of priorities has been, and continues to be, one of the main reasons why most organizations have a very high “Cost Of Quality”. This is in effect, a truly Professional Tragedy of epic proportions.
There was a very famous movie called “Karate Kid” (not the new one but the original one released in 1984) where a very nice and calm old man by the name of “Miagi San” becomes the tutor of a troubled young kid. There is a scene where Miagi san is sitting in a room where he is using chop-sticks to catch mosquitoes flying about. When the kid arrives, Miagi san suggest him to do the same as it would improve concentration. Miagi san goes on to explain that he has been doing this for years and manages to catch about one to two mosquitoes in a month. When this kid starts he catches one mosquitoes in the very first try. Funny as it may be, you would automatically know that it was a fluke and happened by chance and in no-way this incident coulf be taken as a standard. Now compare this case with how professionals react to that “One Good Project” or “One Good Incident” as if that could be made into a standard. In effect we behave as if the “Kid” was better than “Miagi San” as the Kid caught a mosquito in its first try just by chance.
Getting back to my NCC days, I am sure you will understand why our commander always preferred cadets with “Consistent Shooting” over cadets who were inconsistent even if they got more bullets in the bullseye. It was the consistent cadets that he trained to become crack shots and the rest is history as our NCC team won every single shooting competition in National NCC meets and once we even had a friendly competition with the local police department and defeated them as well.
Ok so this takes care of only two of the three terms we set out to explain. The third term is Excellence. Excellence has different meanings in different verticals and only some of them are correct. Most of the meanings floating around for the term “Excellence” are impractical and more like a wish-list and a whim of fancy. I will use this term with the background of Quality and Projects.
“When a process achieves consistent accuracy, it has achieved excellence”. ©PM-Pulse Authored by Maneesh Vijaya, PMP.
Excellence could be a moving target as well and we could increase process excellence by making the targets more granular or the process benchmarks even more refined. This is what is the whole purpose of the Six Sigma projects and initiatives. Once in NCC we got very good at being crack shots, our commander increased the distance between our shooting positions and the targets and brought even smaller targets. Once we achieved “Excellence” in shooting those targets as well, he started to get us to shoot a single “Playing Card” from a distance of 50 Meters in such a way that all 5 bullets pierce it but at the same time it did not disintegrate it or break it apart. None of us could stay in NCC long enough to achieve this level of excellence, but I guess you get the picture of what exactly are we talking about here.
To sum it up, your organization wants to achieve Excellence in project management then it has to first concentrate on “Consistency” even if you are consistently wrong. Having optimized your consistency (precision) over time would help your organization move towards accuracy in a consistent way thus achieving “Excellence”. Excellence could also be improved by making the targets more ambitious and benchmarks more granular.
You will be amazed at the number of organizations which overlook this simple and yet effective sequence of process maturity and thus are in turn contributors to a “Professional Tragedy” of Global Proportions.