Empire State Building Project
Almost everyone knows that Empire State Building was once the tallest building in the world and that it still stands tall in Manhattan, New York and that its observation deck has been a popular site in many major motion pictures. However what people do not know is that this was opened to public in May 1931 and was constructed in just under 18 months flat. Less than one and half years. Compare that to the buildings being constructed today, where the architect and the project manager is armed with software, advanced supply-chain processes, amazing communication tools like virtual presence and cell phones and even guidance from space about terrain mapping and laser controlled tilt warnings and yet most of the building projects run behind schedule and end up being over budget.
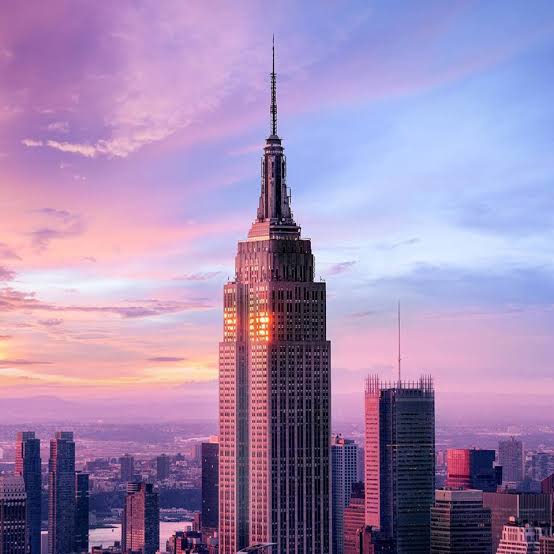
Unfortunately the Empire State Building’s iconic structure and magnificence over-shadowed the project management brilliance that hardly any project professional ever looked upon it as a source of project management lessons that could be replicated at other places.
PM-Pulse goes deep into the background and the environmental factors within which John J. Raskob, his architecture team from the firm Shreve, Lamb and Harmon, the contractor Starrette Brothres and Ekene and the chief engineer Homer Gage Balcom used some of the non-traditional project management and revolutionary supply chain processes to pull off one of the fastest buildings of such mega proportions ever constructed. Let us have a look.
How the idea of Empire State Building came into being?
John J. Raskob (henceforth called Raskob) sold his stake in General Electric, something he had inherited, to pursue his own dreams of being one of the most savvy hoteliers and property owners in New York. Around that time there was this grandest hotel in the world called “Wladorf – Astoria” in Manhattan that had become old and dated and their owners were wanting to sell the same. Raskob thought that this opportunity was a godsend and bought it or USD 16 Million in mid 1928. In his hurry to buy the property he did not conduct detailed due diligence, only to learn later that the local government had already condemned the building and was slated for demolition. You can very well imagine what he must have gone through. The Old Receptionist at the lobby in Empire State Building (I had visited that place about 2 years back again) had told me that “Raskob” went under depression during those days because of having lost almost all his inheritance in one failed gamble. However, with the help of his wife and friends he realized that even if the hotel was being demolished, the site itself was amazingly located. He decided to make a much taller building there, so that the room rates from the new taller hotel would soon overtake the losses that he had suffered. But by that time the elite clientele and the luxury stores had moved further north of Manhattan and several amazing hotels had already come up there, attracting the best clientele. Raskob dropped the idea of a hotel and decided to build one of the tallest office buildings on that site and thus was born the idea of the Empire State Building.
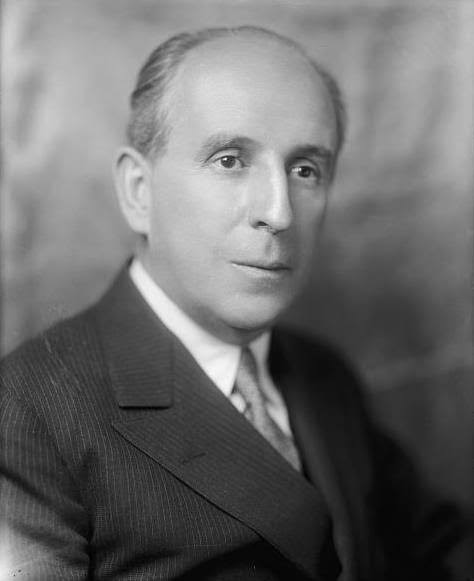
Project Ideation
In late 1928 Raskob started scouting around for investors who would loan him money for his signature 60 story office building that would be the tallest office building of its time and become the landmark for Manhattan. Several banks and financial institutions showed interest and some even offered lower interest rates just to be associated with this prestigious project. However just a week later, just days before signing the contract with two financial institutions the famous “Stock Market Crash Of Wall Street” (also called the Black Firday, different from the now popular Black Friday of 22nd November for discounted sales near Thanksgiving holiday) leading to a loss of USD 50 Billion in just one day and which heralded the infamous “Great Depression”.
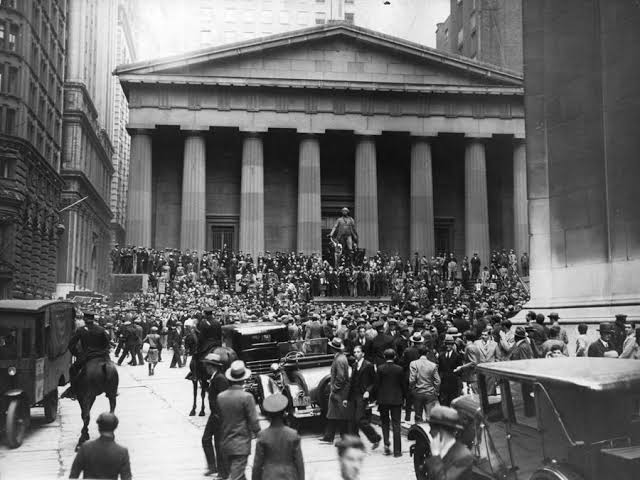
Raskob somehow withstood this double whammy and continued to scout around for financers. He finally got a finance proposal from Metropolitan Insurance as they were not so badly affected by the stock market crash and had some cash reserves. However due to the market conditions they decided to make the interest excessively high and the repayment schedule excessively tight. Seeing no option whatsoever Raskob took the deal and decided to build the entire building in just 18 months to beat the interest charges and meet the repayment schedule which stared after 24 months of disbursement. There was no building ever that was constructed anywhere near this speed and nor was Raskob had any kind of Civil Engineering experience. This was his first project ever.
Project Initiation
In Early 1929 Raskob decided to build an office building about 50 stories high within a budget of 50 Million. With this basic scope and high level requirements Raskob started selecting an architect and the chief engineer. He selected a Chief Engineer from Chicago by the name of Homer Gage Balcom who had become somewhat famous in reconstructing houses and replacing them with taller buildings (called skyscrapers those days) following the infamous great fire of Chicago. Raskob mainly selected him for his aggressive attitude towards construction. The first and the only architect that Raskob met was hired to start documenting all the requirements and start working on the architectural design.
The three of them decided to be the project management core team for the Empire State Building Project and start planning for somehow finishing it in just 18 months.
Planning
Raskob immediately told the engineer and the architect to make a design that was both, elegant and “repeatable”. Today’s term for “Repeatable Design” is called “Componentized Architecture” and in civil engineering its called “Pre-fabricated Design”.
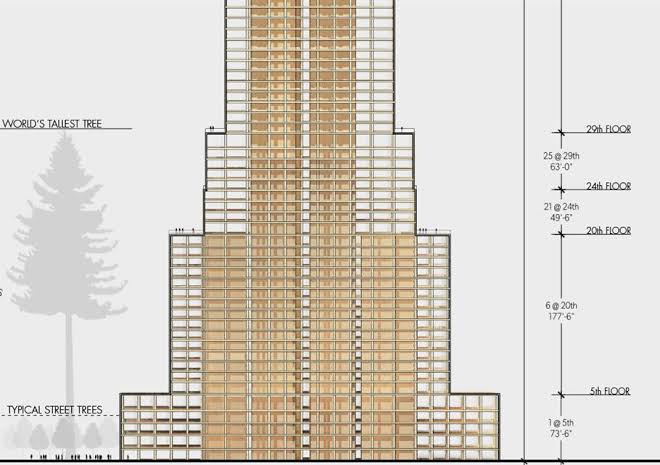
These three (supported by a small and dedicated team of draftsmen) would work day and night going over their design and drawings and measurements again and again. They say that the drafting room threw away nearly 2 tons of paper in cancelled drawing and revisions. Remember, there were no computers or software based modelling. Even a small change in the size of a room or the angle of any supporting arch would lead to redrawing the entire building to understand the impact of the same. They soon realized that this was a great opportunity to make a landmark not only for the city of New York, but also the entire world. This lead to the team pushing themselves to add more floors and increased the floors (in design from 50 to 60 and again to 80 and finally to 92 floors). Each time the drawings for the entire building would change. However since the entire design was based on “Components” the redrawing effort did not take as much time as a more traditional design would have taken.
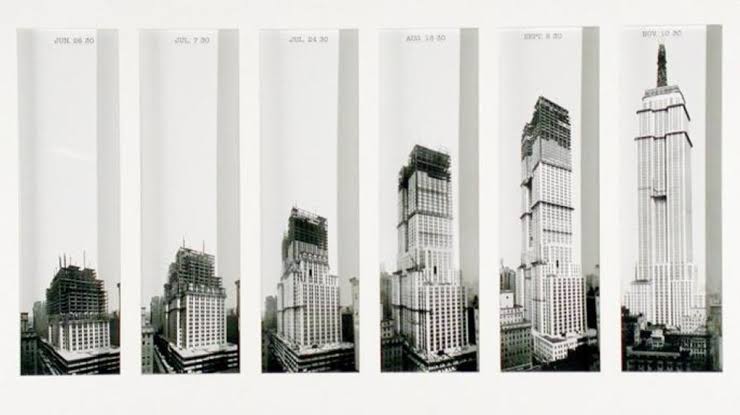
The Architect created the concept of visual drawings for story telling (something that is known as “Story Board” in Agile and Movie industries) to visually show and plan how the empire state building would be built and how would it progress. Where would the entrance be, where would the people park their cars, where would the construction material be kept and where would the cranes be placed. Where all the cranes could not move their arms due to other nearby buildings and so on.
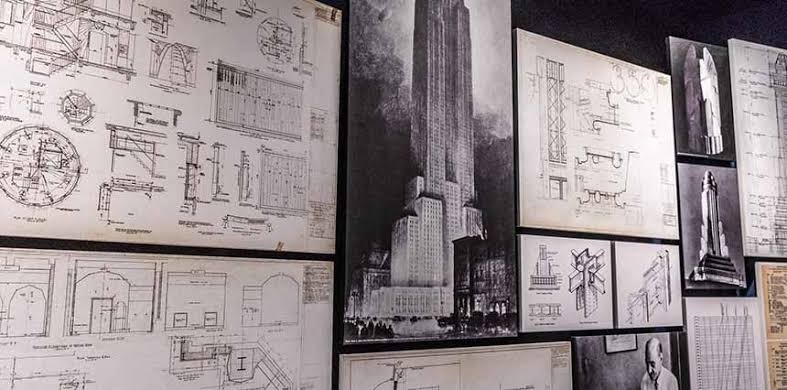
Since this was the first building that would be this high, they decided to make the top of the building narrower than the bottom part thus creating a “Pencil Shape” layout that not only maintained a low centre of gravity but also looked very elegant and majestic even though there are no ornate work done on the external façade of the building.
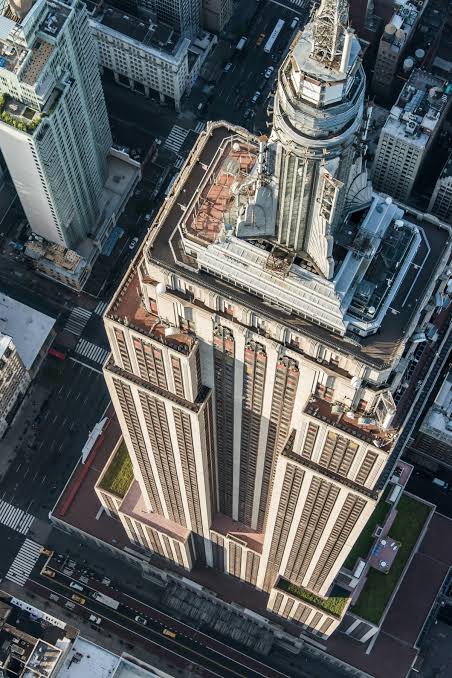
New York times got a hint of what Raskob and his team were doing, divulged the idea in News Papers. Not only this, they went on to come out with a reward and recognition to anyone who could make the tallest building in the world before the end of 1931. This changed everything. Chrysler Corporation got into this fray as they had much reserve cash and one of the builders on 40th Wall Street, having acquired a site from a crashed Wall Street firm at dirt cheap prices, openly challenged Empire State team.
Raskob and his team changed their drawing all over again to try and pull the building taller. They came to know that Chrysler was planning a building that was nearly as tall as them, and that once the project would be completed Empire state building would be only 4 feet taller than Empire State building. To this the chief engineer pointed out that since Chrysler building had a tower at the top, all they had to do was to keep a steel rod hidden inside the tower and just at the time of New York Times survey, could push that rod out through the tower making them technically taller than us. The team decided to add more floors and another 16 floors tapered crown like structure at the top and also make a 68 meter tower for docking of “Airships”. But they also decided not to start the construction.
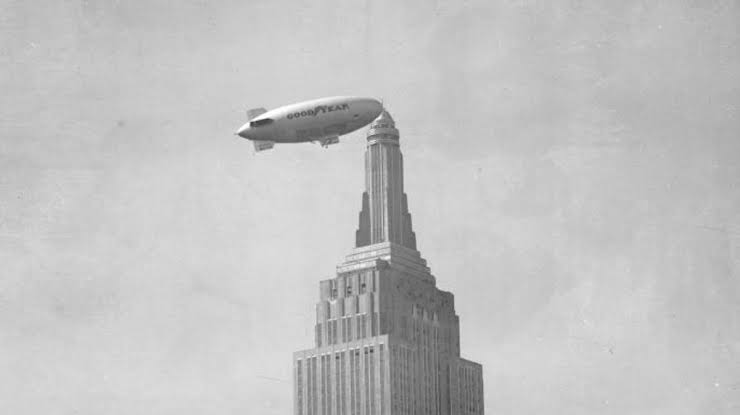
They let Chrysler start their construction and lay their foundation. Once that was done Chrysler had to commit to the drawing and would not be able to alter the design midway. Hence the Empire state waited for 4 more months to start construction and decided to re-plan so that now the construction could be done in just 14 to 15 months.
The project team made a very detailed Work Breakdown structure that was so detailed that not only the exact numbers of steel girders were known, even the numbers of rivets that each of the girders would have were known and numbered.
They worked with surrounding foundries to develop a plan where the girders would be made in a “design-linked” schedule where specific kinds of girders in specific numbers would be made in lots such that the supply of girders to the site would match the kinds of girders needed at different stages of completion of the project.
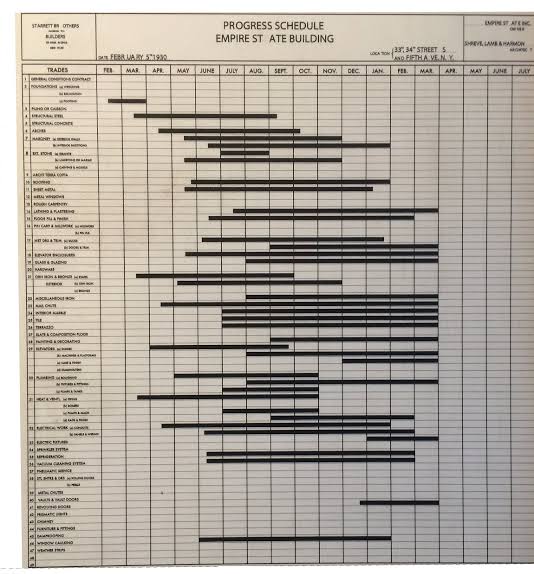
They also worked out a code marking system with the foundries where each of the girders leaving the plant would have a design code which would mean which crane would lift it at site and place it on which floor and also which corner of that floor would the girder be placed. Besides, since the entire design was a “Repeatable” architecture, the project team contracted with marble providers, concrete providers and window makers to start working on specific shapes and sizes in specific numbers and start accumulating finished components at their own warehouses. The construction of these material parts was to be done in “Top of the Building First” basis so that the material needed at the bottom most part of the building, once the construction actually started, would be the easiest to pick up from the warehouses.
The most impressive labour contracts was done by Gage who only hired US nationals as labourers instead of the cheaper immigrants as most of the US labour were more skilled in high rise buildings and were used to rough weather conditions towards the higher side of the building. He also struck some labour contract alterations where lesser number of people would work for longer hours and instead of being paid with overtime they would be provided with result based incentives, which if achieved, would be higher than the overtime rates.
Once the Chrysler building started constructing over its foundation, Empire state building started construction.
Project Implementation
Construction officially started on March 17, 1930. Already 4 months behind schedule, though purposefully.
Because of the amazing level of detailed planning and armed with highly motivated labour forces (who wanted to make money during the great depression and also wanted to show to the immigrant labourers their own superiority in work quality) and consistent fail-proof supply of material from all vendors in “clock-work precision” the speed of construction moved up to as much as 4 and half stories every week. Soon a competition started between different shifts which pushed up the speed so much that once the rate of construction reached over 14 and a half stories in just 10 days.
Labour supervisors were armed with the schedule and code for which part of girder or window or pre-fabricated wall or pre-fabricated flooring slabs of marbles, would go where. As the infra-construction labourers moved upwards the façade ad interior building labourers would simply slide in the highly calibrated pre-fabricated material in the lower floors. Immediately after the interior work labourers the utility labourers for phones, electrical wires, plumbing etc would move in and just as they would finish the final finishing workers would move in. This chain of “Ant-work” relay work kept on moving upwards a floor at a time.
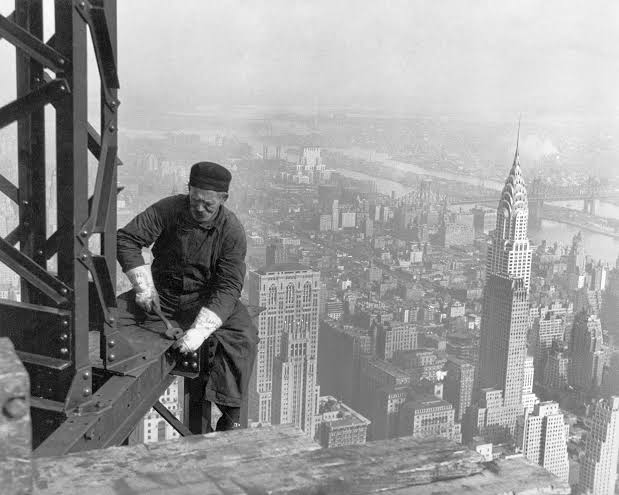
The project core team would have a daily meeting with at least two of the members of the core team present to assess what they could achieve till yesterday, what challenges they faced today, how much money was saved till now and what was the projected outlook of finances outflow till completion. This ensured that everyone was on the same page and be critically aware of work priority at any point of time.
After just 410 days of construction (March 17 1930 till April 11, 1931) the building was almost completely ready. So ready that the building could be thrown open to public in just one month of completion viz., May 1, 1931 (something unheard of even today).
During the implementation phase, Raskob did another great initiative. He came to know that one of the first high-quality lifts were being tested in Beever Building in New York, he partially financed the testing by building artificial and temporary extended structure above the Beever building to see how well the lifts worked in higher buildings. He did that so that time would not be wasted for testing at his own building. This gamble worked so well that hardly any adjustments needed to be done when the lift system was actually fitted in the Empire State Building.
However, there was a darker side to this journey. Though substantial risk management was done, the risk management was not done well towards the risks facing human life. Human life in US was quite cheap during those days specifically for the labour working in mining, manufacturing and construction. A total of 14 lives were lost during construction. However those days it was written in New York time as an achievement of having lost “only 14 lives”.
At the peak of their work this project employed 3,400 workers who put in 7 million man hours of work.
Work was completed USD 9 Million under budget and 3 months before schedule.
Project Closure and Handover
The core project spent over 10 days to document all their learning as they were hugely emboldened by this success that they wanted to repeat it multiple times. However this could not happen as Raskob’s eldest of his 13 children died in a car crash in 1931 and he suddenly changed his direction to philanthropy and public service instead of making more construction projects.
The handover was one of the smoothest. Not a single hitch happened on the opening day. When New York Times came for survey using a mathematician to find out whose building is taller, Raskob told them to “Stuff their mathematics in your… “ ( I guess you know where) and invited to them to come up to their observation tower to “Look Down On the Chrysler building”.
New York Times played a bit of a villain, because Chrysler used to publish a lot of advertisements in NYT, by publishing an article that questioned the construction quality and safety while praising the fastest construction and for being the tallest building in the world. This affected their immediate sale of offices but soon that myth was also broken and within 2 yrs the Empire State Building had full occupancy.
The real test of its strength was found out on July 28th 1945 when a B-25 Mitchell Bomber (with bomb payload) crashed into the Empire state building at 9:30 am, a time when offices were full of working people.
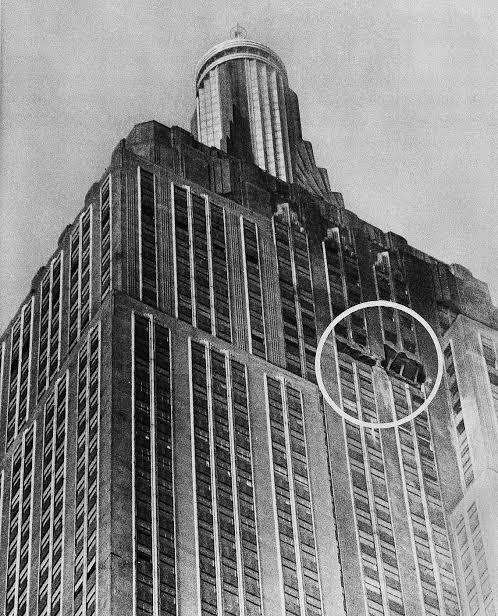
It crashed between 60th and 70th floor and created a huge crater 18 feet high. Even though the bombs exploded and the fuel was seeping into the floors and burning, most of the aircraft was disintegrated outside of the building and fell to the ground in front of the building. 14 people died. Several floors came to know of the crash much later as there were hardly any vibrations due to crash, at the lower floors.
This however makes me wonder (and I am sure most of the other more intelligent variety of people) how, a much lighter, passenger planes could bring buildings (3 times stronger than Empire state building) crashing down into their own foundations without tipping over.
There are some amazing lessons that we can learn from this project:
-
Nothing beats simplicity of idea (irrespective of how complex the execution is).
-
Project scoping and clear expectation setting can make the difference between success and failure.
-
Fixing of priorities and unabashedly sharing it with every key stakeholder ensures a unification of the decision making process at every level.
-
WBS is the most powerful tool of project management and one of the sole reasons for componentization and providing agility to your project work.
-
Effort spent on detailed scheduling never ever goes to waste.
-
Spending more time on effective and detailed planning always gives benefits (financial and otherwise)
-
Vendors are project partners from other organizations and planning with them works better than planning for them.
-
Desperate situations could be used for focusing only on what is important and help you develop some critical thinking and Out – of – the – box solutions.
-
Highly motivated and skilled project team always outperforms a team that is just larger.
-
Sponsorship means taking deep interest in the project without coming in the way of the project team. It’s about providing directions and making decisions instead of micro-management.
-
Follow the processes so that you can re-invent them for the future work.
-
Practical project management and simplicity of ideas are far better than empty jargons and qualifications.
-
Project Management tools and software do not replace project management they are just tools with project managers. “A Fool with a Tool is still a Fool”.
-
PMP and Agile certification are important but they are not the only measure of a good project manager. Project Management is a way of living and thinking and is closely related to critical thinking.
-
Problem solving is a constant in project management. Managers who embrace it tend to do better in project management.
-
Power of project management is in shared vision and not in delegation of vision.